I am honored to expose myself into various co-op experiences, specifically as a Quality (Sanofi), Process (Amphenol CTI), R&D (Amphenol TFC), and Manufacturing Engineer (Lavo).
​
These roles were deliberately chosen to expose myself to different facets of mechanical engineering, allowing me to gain a comprehensive understanding of the entire product design process and the collaborative nature of engineering roles from typical product development procedures - product design (R&D), process design, manufacturing, quality assurance. I equip myself with a holistic perspective of mechanical engineering.
This comprehensive understanding of various roles and their interdependencies has instilled in me a deep appreciation for collaboration and cross-functional teamwork, which I believe are critical elements in delivering superior engineering solutions, as well as my future career.
09/2021 – 08/2022
CV Co-op Student
​
Manufacturing Technology
Sanofi Pasteur

• Generated study reports, SOPs for DPT vaccine manufacturing procedures, achieved 20% increasing in reliability
• Validated cleaning solutions by data analysis techniques, obtained 100% compliance with FDA standards
• Established SWI system by applying 5s, 6-sigma, GLP for lab environment, doubled working efficiency in the lab
• Monitored production statuses by sampling and testing vaccine by-products, with 0 deviations against SOPs
• Managed CV lab, conducted equipment MSA, ensured the 100% alignment with FDA and SOP regulations
05/2020 – 08/2020
Process Engineering Intern
​
Engineering Technology
Amphenol CTI Industries Inc.

• Led the drafting of cable assembly process using AutoCAD, project completed ahead of schedule by 10% of time
• Performed Root Cause Analysis to assess manufacturing downtimes, increased TPA by 20%
• Qualified OEM parts & BOM in conjunction with R&D and operators, cut down on mistakes by 10%
• Maintained and updated DHF and DMR files, ensured alignments with product specifications with 0 errors
05/2019 – 08/2019
R&D Engineering Intern
​
R&D Department
Amphenol TFC Communication Equipment Co.
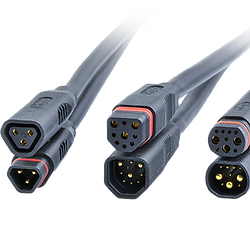
• Designed water-proof connectors by considering GD&T for Bosch e-bike wiring system using SolidWorks
​
• Led the running trials of connectors by single-cavity injection modelling technique, eliminated injection-modelling errors by performing Root Cause Analysis, accomplished 0 bad batch in MP stage
​
• Supported all stages of product development including conceptual design, EVT, DVT, PVT of connectors
05/2018 – 08/2018
Manufacturing Engineering Intern
​
Manufacturing & Operation
Lavo Manufacturing Ltd.
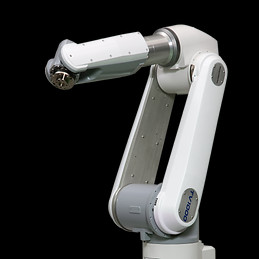
• Optimized manufacturing processes for components, achieved 15% down on material consumption
​
• Integrated PLC systems to control various manufacturing equipment, optimized production efficiently by 10%
​
• Utilized the capabilities of a 6-axis robot to automate to perform drilling tasks, batch delivered ahead of schedule
​
• Maintained detailed production records, including work logs, production reports, and quality control documents