Project Two
WaveGen Technology Inc. has proposed a solution to improve system efficiency by re-arraying the WECs according to wave conditions, ensuring that wave interference generated by other buoys superpose with the actual wave is considered.
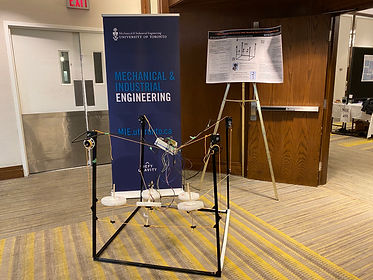



Autonomous WEC Relocation System
Project Overview
The Capstone Design course held paramount significance in our university journey. Our team was fortunate to collaborate with Professor Chandra and WaveGen Technologies Inc. to address the inefficiency problem in the WECs system through the relocation of the second line of WECs.
As the team leader in this project, my primary responsibility was to steer the team towards success, which encompassed the development of a successful prototype and leaving a lasting positive impression on both the client and Professor Chandra.

Design Specification
Frame
To achieve this, I have laid the foundation of the mechanical system using 2020 aluminum extrusion bars. These bars provide a convenient and adjustable platform for fixing all the components in place.
​
​
​
Pulley System
The pulley system consists of a large and a small pulley connected by a timing belt. The small pulley is connected to the motor's output shaft, while the large pulley is connected to the cable collector. With the new pulley system, the stepper motors can provide sufficient power to move WECs accurately and also a high stalling torque to hold WECs’ position after movements.
​
To ensure the proper functioning of the pulley system, bearings are used with 3D-printed casings to support the shafts and reduce friction. Additionally, the casing was designed to be assembled onto extrusion bars with T-nuts. The height adjustable feature helps to maintain correct tension in the timing belts, ensuring smooth operation and preventing belt slippage.
Tensioned Cables
The cables are selected from corrosion-resistant, high tensile strength material, Polypropylene, to withstand the harsh water environment.
​
The end of cable is fixed on to cable collectors driven by stepper motors, the cable guiding components (shown in Figure 12) are assembled onto corner posts with T-nuts. By changing the height of the cable guiding parts, the height of buoys can be adjusted to perform in various water depth from 30cm to 80cm.
Testing Result
Land Testing

Water Testing
Final Result
"The successful outcome of the prototype has demonstrated the viability of commercializing the WEC system."
— Nishanto Pishon, CEO of WaveGen Technologies Inc.
​
The successful creation of the Autonomous Mooring of WECs prototype has unequivocally demonstrated the feasibility of this groundbreaking technology.
​
Against the backdrop of climate change, harnessing ocean energy becomes imperative, especially when the technology reaches a level of maturity. I take great pride in being able to contribute my efforts towards the commercialization of this transformative technology.
​
​